Des composites innovants pour ouvrir de nouveaux marchés
Bien que la base de l'entreprise soit très certainement l'enroulement filamentaire, CompoTech a poussé ce processus dans de nouvelles applications via l'enroulement à base de broches, le surenroulement et des concepts innovants d'outillage et de matériaux. Le résultat est une fluidité dans le processus qui atteint souvent de nouveaux niveaux de performance via l'hybridation, par exemple, avec des métaux et des méthodes de fabrication comme l'impression 3D et sa propre version de pose automatisée de fibres (AFL).
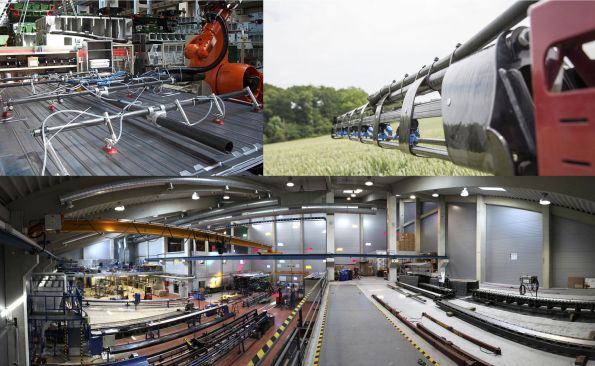
CompoTech produit des pièces pour une large gamme d'applications, y compris les équipements industriels (ensemble de pinces à vide, en haut à gauche) et les équipements agricoles (rampe de pulvérisation, en haut à droite) depuis ses installations de Sušice, en République tchèque (en bas). SOURCE :Bilsing Automation (pince, en haut à gauche), Hardi International (rampe de pulvérisation, en haut à droite) et CompoTech.
CompoTech (Sušice, République tchèque) a été fondée en 1995 par Ondrej Uher et Vitek Sprdlik, respectivement directeur R&D et directeur technique de la société. « À l'origine, ils ont construit une machine d'enroulement filamentaire pour produire des tiges de pagaies de kayak et de canoë qui intégrait leur propre technologie pour l'enroulement axial des fibres à 0° », explique Humphrey Carter, directeur du développement commercial de CompoTech. « C'est désormais une compétence de base. Nous avons montré que cette construction produit des structures plus solides et plus rigides avec une plus grande résistance au flambage des fibres. »
L'entreprise a également développé la capacité d'enrouler des arceaux composites intégraux pour les connexions. Ceux-ci sont utilisés dans des pièces allant des longerons de deltaplane aux arbres de transmission et aux composants industriels. « CompoTech conçoit les machines et le logiciel de contrôle », explique Carter. « Parce que nous avons le contrôle total du processus, nous pouvons mieux optimiser la conception. Nous développons la technologie de processus sur mesure selon les critères de conception et pouvons la mettre à disposition de nos partenaires technologiques ainsi que des concepteurs et producteurs de composites. Par exemple, nous avons concédé la technologie sous licence à Southern Spars/North Marine Group. »
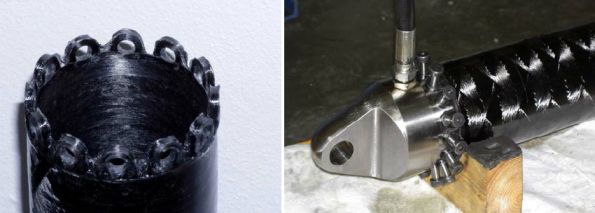
CompoTech enroule la fibre autour des broches (à gauche) pour produire des structures
avec connecteurs intégrés (à droite). SOURCE :CompoTech
Conception de machines-outils
Actuellement, l'entreprise emploie environ 50 personnes, dont près de la moitié dans la conception et l'ingénierie. Il entretient également des liens étroits avec l'Université technique tchèque (CTU) de Prague ainsi qu'avec l'Université de Bohême occidentale (Pilsen, République tchèque). CompoTech a développé des solutions composites pour une large gamme d'applications, notamment des rampes pour équipements de pulvérisation agricole, des arbres pour les pointes de pales d'éolienne, des cadres et roues de bicyclettes, des tubes et des cadres pour les pinces d'assemblage automobile et des composants de portique légers pour les découpeuses laser et les machines CNC.
« Nous travaillons depuis le début des années 2000 dans le secteur industriel et de la machine-outil en raison de sa prévalence en République tchèque », explique Carter. « C’est une industrie très conservatrice qui ne connaît pas les composites. Ainsi, nous allons à des expositions de machines-outils et les éduquons. Cette industrie sait déjà que les vibrations des pièces en accélération et des surfaces de coupe, telles que les dents de fraisage, entraînent une réduction de la précision d'usinage et de la durée de vie de l'outil. CompoTech explique que les harmoniques d'un outil de coupe - ses vibrations basées sur la masse, la rigidité et les charges/forces appliquées - sont souvent le facteur limitant des performances et de la productivité. On ne sait pas si bien que le plastique renforcé de fibres de carbone (PRFC) peut être utilisé dans la structure des machines et des porte-outils pour réduire la masse et augmenter la rigidité par rapport à l'acier. En utilisant la fibre de pitch, CompoTech rapporte une réduction de poids de 25 % et une augmentation de la rigidité de 200 % (400 GPa obtenus avec la fibre unidirectionnelle), respectivement. Ce sont les deux principaux moyens d'augmenter la fréquence naturelle d'une structure et d'empêcher la résonance. C'est à ce moment-là que la structure vibre d'elle-même, ce qui aggrave les problèmes des pièces rotatives et des machines à vitesse variable déjà sujettes aux vibrations.
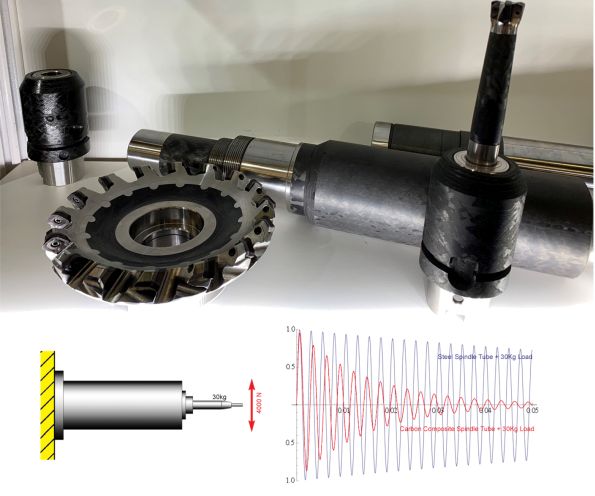
CompoTech utilise CFRP et des matériaux d'amortissement supplémentaires pour réduire le poids et augmenter la rigidité et l'amortissement par rapport à l'acier afin d'éviter les vibrations. Leur technologie réduit également la dérive de la machine-outil, ce qui améliore les performances d'usinage et la productivité. SOURCE :CompoTech
« L'utilisation de notre procédé pour CFRP réduit également la dérive des machines-outils par rapport aux composites autoclavés, car nous induisons moins de contraintes thermiques », ajoute Carter. « Les porte-outils sont souvent des poutres longues et minces qui peuvent changer avec le temps, en fonction de leur conception et de la composition de leurs matériaux. Cela affecte alors la position relationnelle de l'outil, réduisant sa précision. »
Pour l'amortissement, CompoTech est allé au-delà des propriétés inhérentes des composites de fibres et de polymères pour intégrer d'autres matériaux, fournissant 12 à 20 fois l'amortissement de l'acier, contrant directement les vibrations et agissant pour accélérer sa dégradation (voir graphique ci-dessus). « Nous avons plus d'une décennie d'expérience dans la conception de composites amortis pour obtenir les propriétés et les performances souhaitées », déclare Carter. Un exemple est une nouvelle conception de mandrin de pièce de sorte qu'une force de serrage beaucoup moins importante est requise par rapport à un mandrin en acier. Un autre est le montage modifié pour le tournage d'un carter de turbine basse pression (LPT) de moteur d'avion fabriqué à partir d'un alliage Inconel 718 difficile à usiner. Développé dans le cadre du projet INTEFIX financé par l'UE, CompoTech a développé des anneaux CFRP pour remplacer les anneaux métalliques utilisés comme localisateurs dans le luminaire. Le résultat n'a été aucune perte de rigidité ou de fonction tout en améliorant le comportement de la pièce et de meilleures performances d'usinage. En effet, le montage a été rendu intelligent, capable d'adapter le serrage de la pièce selon les besoins au cours du processus.
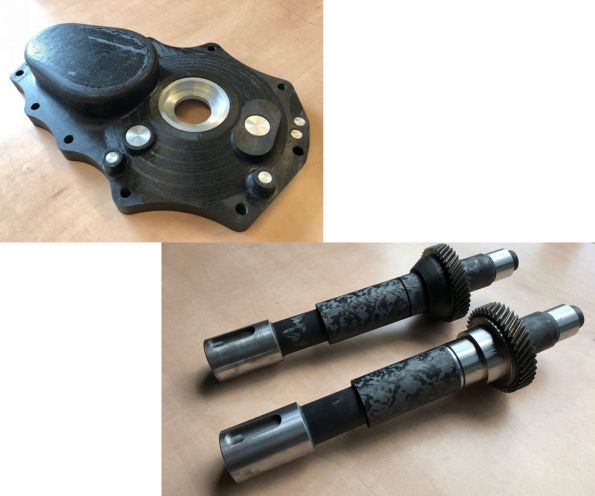
CompoTech a développé , en collaboration avec CTU, KIMM et Samyang Reduction Gear, une boîte de vitesses et arbres de transmission hybrides métal/composite pour véhicule électrique offrant un poids et un bruit réduits. SOURCE :CompoTech
CompoTech travaille également en cours sur une boîte de vitesses hybride métal/composite de véhicule électrique, visant à réduire la masse de 25 % et également à réduire le bruit en augmentant la fréquence naturelle et l'amortissement. Ce projet (2016 à octobre 2019) est en collaboration avec l'Université technique tchèque (CTU) de Prague, le Korea Institute of Machinery and Materials (KIMM, Daejeon, Corée du Sud) et Samyang Reduction Gear Co. Ltd. (Inchon, Corée du Sud). Le corps principal de la boîte de vitesses sera en composite avec des inserts métalliques pour les surfaces d'appui. CompoTech a conçu et produit le carter supérieur et inférieur de la boîte de vitesses, ainsi que les arbres de transmission. Tous sont composés de plusieurs pièces collées. La CTU a fourni les tests et l'analyse FE, tandis que les partenaires coréens du projet fournissent les spécifications techniques et termineront, assembleront et testeront les boîtes de vitesses.
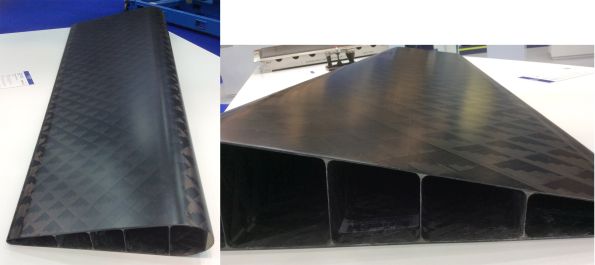
CompoTech a développé un aileron monobloc utilisant un enroulement filamentaire et des nervures longitudinales - au lieu des nervures de cloison conventionnelles, du préimprégné et du collage - résultant en une structure légère et résistante au délaminage, en particulier au bord de fuite.
SOURCE :Ginger Gardiner, CW au JEC 2019
Aileron résistant au délaminage
Carter explique qu'une grande partie de la R&D effectuée par CompoTech pour les machines-outils est ensuite appliquée à de nouvelles applications, comme l'aileron pour le jet trainer L-39NG d'Aero Vodochody AEROSPACE (Odolena Voda, République tchèque). « Il s'agit d'une application exigeante, avec des pressions très élevées au bord de fuite », dit-il. En plus des charges de vol, la version armée de l'avion subit des ondes de pression lorsque des roquettes montées sur les ailes sont tirées. « Avec la construction composite conventionnelle, il y avait un délaminage au bord de fuite des ailerons », note Carter. « Nous avons éliminé tous les collages et avons créé à la place une structure intégrale en utilisant un enroulement filamentaire humide et un co-durcissement. Nous avons passé des mois à développer les étapes de conception et de processus. Tout d'abord, notre enrouleur assisté par robot est utilisé pour enrouler en filament les quatre poutres caissons qui forment les longerons d'ailerons. Ce sont des trapèzes, puis des formes en D sur les bords avant et arrière. Le bord de fuite a également une pièce séparée pour créer une surface plus aérodynamique.
« Nous joignons ensuite toutes ces pièces sur leurs mandrins ensemble et survent pour créer les surfaces extérieures au-dessus des nervures longitudinales », poursuit Carter. L'ensemble de la structure est mis sous vide et durci à température ambiante avec un post-durcissement à 90°C.
Ce projet est un bon exemple de la façon dont nous travaillons avec un client pour développer la technologie et la conception du processus. Notre idée n'est pas de produire en série des ailerons ou d'autres pièces. Nous produisions les machines et nos clients enrouleraient les pièces. L'aileron vole maintenant et Aero Vodochody a un carnet de commandes de 4 ans pour les commandes d'avions d'entraînement à réaction L-39NG.
En général, le processus de bobinage humide de CompoTech est basé sur la précision, créant essentiellement du towpreg à la volée. « Nous utilisons principalement des résines époxy et un durcissement à 100 °C », explique Carter. « Pour les applications nécessitant une Tg plus élevée, telles que certains outils de fond de trou que nous avons produits pour une utilisation dans l'industrie pétrolière et gazière, nous pouvons durcir à 140 °C. »
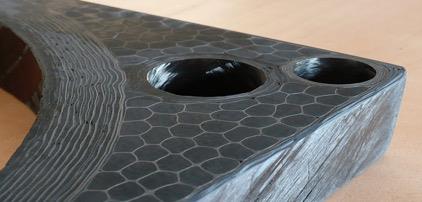
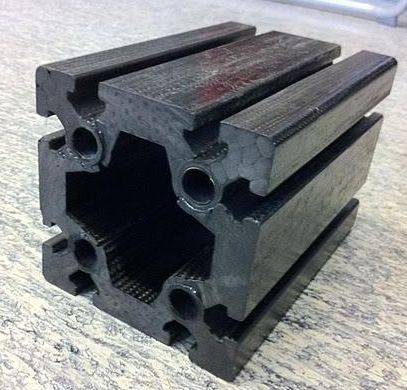
Exemples de 3D composites alvéolaires pour haute rigidité axiale, pièces sectionnées épaisses et complexes. SOURCE :CompoTech
Nouveaux processus
Le composite cellulaire 3D (3Dc) est le nom de CompoTech pour une série de processus qui produisent un composite avec un renforcement tridimensionnel. Résultant en une section transversale avec un aspect cellulaire, cette construction atteint une teneur élevée en fibres axiales dans la direction x interconnectées avec des fibres dans les directions y et z, qui forment les parois cellulaires. Nous avons créé ce procédé pour les pièces épaisses qui nécessitent une rigidité axiale très élevée », explique Carter. Cette rigidité est créée par la teneur très élevée en fibres de 0° (axial). Les parois cellulaires supportent également une charge de cisaillement à travers la section via les parois cellulaires et permettent de réaliser des sections plus intéressantes, telles que la rainure en T illustrée ci-dessus.
La société imprime également en 3D des mandrins et des supports pour répondre aux exigences de torsion et de fréquence naturelle sans stratifiés plus épais. « Il s'agit d'un autre projet en collaboration avec la CTU », explique Carter, « où nous développons une conception interne automatisée des structures. » Il constate que le bobinage des composites thermoplastiques est en plein essor. "C'est notre prochaine étape, combiner notre enroulement dans les thermoplastiques avec l'impression 3D et utiliser le pliage pour créer des outils de moulage innovants pour les composites ainsi que les structures de machines-outils."
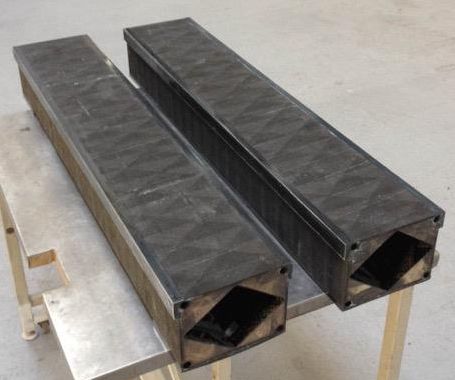
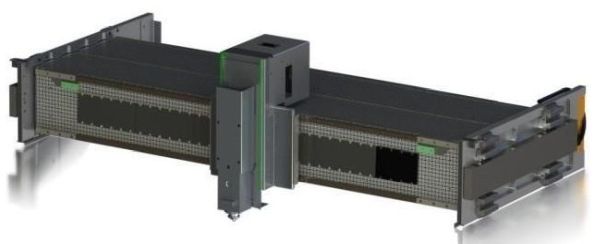
CompoTech utilise des processus pour créer des structures de portique CFRP rigides et légères qui améliorent la précision et la vitesse de la machine. SOURCE :CompoTech, Eagle Laser.
Résine
- AT&T et Tech Mahindra collaborent sur une nouvelle plateforme d'IA open source
- CompositesWorld SourceBook 2022
- La nouvelle botte de randonnée Salewa est dotée de composites thermoplastiques
- CEAD lance un nouveau robot extrudeur E50 pour les plus grands composites imprimés en 3D
- Les nouvelles technologies et les marchés à World of Filament événement Winding
- Le consortium IRG CosiMo sur les composites thermoplastiques dévoile de nouvelles installations
- Green Science Alliance Co. Ltd. fabrique de nouveaux composites de nanocellulose
- Composites hautes performances en Israël
- Nèos International établit un nouveau siège, une usine de composites au Royaume-Uni