Fibre de carbone/époxy pour la réduction de masse automobile, production de masse
Le projet IACMI 3.2 a évalué des composites renforcés de fibres de carbone imprégnés d'un nouveau système de résine à base d'époxy pour développer des pièces composites structurelles à géométrie complexe pour remplacer les métaux dans des applications critiques pour la sécurité à haute charge sur les structures de carrosserie primaires des passagers à grand volume Véhicules. L'une des premières applications évaluées a été l'utilisation d'un préimprégné en fibre de carbone/époxy sur le montant B d'un véhicule d'essai. Le matériau préimprégné haute performance a directement réduit la masse de 3 kilogrammes et a permis de réduire le calibre de la tôle environnante, qui pourrait ensuite être spécifiée dans des alliages moins coûteux, offrant un poids supplémentaire et des économies de coûts. Origine | Ford Motor Co.
Les constructeurs automobiles de la plupart des zones géographiques sont confrontés à des mandats 2025 difficiles sur la réduction des émissions d'échappement et/ou l'amélioration de l'économie de carburant pour les véhicules de tourisme. Cependant, le développement d'une technologie automobile fondamentalement nouvelle pour répondre à ces exigences est coûteux, de sorte que des consortiums permettant aux membres de la chaîne d'approvisionnement de partager les coûts de la recherche préconcurrentielle sont utilisés dans de nombreux pays.
Aux États-Unis, l'une de ces organisations est l'Institute for Advanced Composites Manufacturing Innovation (IACMI - The Composites Institute, Knoxville, Tennessee, États-Unis). Parmi les initiatives de l'organisation, les membres de l'IACMI issus de l'industrie, du milieu universitaire et du gouvernement travaillent sur des projets à plusieurs volets - impliquant le développement de matériaux/processus intégrés, la modélisation/simulation, l'assemblage multi-matériaux et le recyclage - pour résoudre des problèmes d'ingénierie, améliorer la masse du véhicule, réduire l'énergie consommation et les émissions, et créer de nouveaux emplois aux États-Unis.
Projet 3.2 et le système de résine impossible
Le projet 3.2 a été l'un des premiers projets entrepris par IACMI lors de sa création en juin 2015, bien que la technologie utilisée dans le projet ait en fait commencé à être développée quelques années avant la création d'IACMI, avec une collaboration entre Ford Motor Co. (Dearborn, Mich. , États-Unis) et ce qui était alors Dow Automotive (maintenant The Dow Chemical Co., Midland, Michigan, États-Unis). Lorsque l'IACMI s'est formé et que le projet 3.2 a démarré, Ford et Dow ont intégré au programme leurs travaux antérieurs sur un nouveau système de résine époxy. Une fois associé à l'IACMI, le programme s'est élargi pour éventuellement inclure plusieurs phases représentant de nouvelles utilisations pour cette résine innovante :un pilier B préimprégné, un couvercle de coffre en composé de moulage tout en feuille (SMC) et un hayon SMC/aluminium.
Appelée VORAFUSE, la famille de résines développée par Dow pour Ford est conçue pour être utilisée dans le préimprégné et le SMC, et pour être traitée sur des équipements de moulage par compression, largement disponibles dans l'industrie automobile nord-américaine. Selon les exigences de Ford, la température de transition vitreuse de la résine (Tg ) est de 150-160 °C, il moule à 145-155 °C et durcit en moins de 2 minutes à 150 °C (bien qu'un durcissement inférieur à 1 minute soit disponible), ce qui le rend suffisamment rapide pour les volumes élevés ( plus de 100 000 véhicules par an). Il atteint des durcissements post-moulage de plus de 95 %. Le système est exempt de solvants et de composés organiques volatils (COV).
« Les CTQ [critical-to-quality requirements] définis par Ford sont uniques et n'ont jamais été atteints dans un seul produit commercial auparavant », explique Dave Bank, membre de la R&D de Dow Polyurethanes. « Pour cette raison, une nouvelle chimie et une multitude de produits hautement non traditionnels étaient nécessaires pour répondre à ces spécifications exigeantes. »
« La séparation thermodynamique de la stabilité au stockage et de la polymérisation dans le mélange résine/curatif donne une pâte sèche qui peut être infusée dans la fibre de carbone sans faire avancer le durcissement et produire un composé de moulage sec et non collant », ajoute Bank. « Pourtant, lorsque les conditions de moulage atteignent 150 °C, la chimie est « chaude » et le durcissement avance rapidement. » Dow a déposé 21 demandes de brevet et a obtenu jusqu'à présent quatre pour cette technologie.
Caractéristiques supplémentaires du système VORAFUSE :
- Il se conserve à température ambiante pendant plus de 50 jours, mais offre un durcissement instantané à ou au-dessus de 150 °C. Il ne nécessite pas de stockage au congélateur avant la découpe et le moulage du kit tant que la température de stockage ne dépasse pas 40 °C.
- Sa chimie non collante est idéale pour la manipulation automatisée. Parce qu'il n'a pas le caractère collant du préimprégné traditionnel, il ne causera pas d'accumulation ni de problèmes connexes avec les robots et autres équipements de manutention automatisés.
- Il contient un nouvel agent de démoulage interne (IMR) permettant aux transformateurs de mouler 1 000 pièces avant d'avoir à appliquer un démoulage externe sur les surfaces des outils. L'époxy est normalement antithétique à l'IMR car c'est un adhésif très efficace pour les métaux.
- Le produit non durci peut être recyclé en pièces de grande valeur en coupant et en réinjectant le matériau dans les systèmes de moulage en tant que composé discontinu renforcé de fibres, idéal pour mouler des géométries complexes telles que des nervures/bosses. Contrairement au préimprégné époxy et au SMC conventionnels, tous les déchets non durcis peuvent être réutilisés, ce qui rend le matériau plus durable et réduit les pertes de déchets qui augmentent les coûts des pièces.
Phase 1 :Pilier B préimprégné
Après l'intégration de VORAFUSE dans le projet 3.2, l'IACMI a commencé à travailler sur une application automobile qui deviendrait la phase 1 du projet global. Les membres de l'équipe comprenaient Ford, Dow, DowAksa US LLC (la branche américaine de DowAksa BV à Tucson, Az., une coentreprise à 50/50 entre Dow Chemical et Aksa Akrilik Kimya Sanayii A.Ş., Çiftlikköy-Yalova, Turquie); Michigan State University (East Lansing, Michigan, États-Unis); Université Purdue (West Lafayette, Indiana, États-Unis); Université du Tennessee-Knoxville (Knoxville, Tennessee, États-Unis); Continental Structural Plastics (CSP, Auburn Hills, Michigan, États-Unis); et Oak Ridge National Laboratory (Oak Ridge, Tennessee, États-Unis).
Dans la première phase, les chercheurs ont développé un préimprégné continu (tissu tressé et non frisé) renforcé de fibres de carbone imprégné d'époxyde. La résine VORAFUSE P6300 a été formulée pour être compatible avec la fibre de carbone à module standard DowAksa A42 D012 24K. L'objectif de l'équipe était d'utiliser le préimprégné en fibre de carbone/époxy pour développer des pièces composites structurelles à géométrie complexe pour remplacer le métal embouti dans des applications hautement chargées et critiques pour la sécurité sur les structures de carrosserie primaires des véhicules à grand volume.
Pour le démonstrateur technologique, le pilier B sur un côté d'une Ford Fusion véhicule d'essai a été utilisé. La viabilité a d'abord été évaluée par simulation, puis les pièces physiques ont été moulées et soumises à tous les tests requis, y compris des collisions de véhicules à grande échelle. Les pièces sont passées avec brio, réduisant la masse de 3 kilogrammes par côté par rapport aux métaux en place. La ferraille non durcie a été recyclée pour former les structures de nervures complexes du pilier. Le composite haute performance a permis de réduire le calibre de la tôle environnante, qui pourrait ensuite être spécifiée dans des alliages moins coûteux, offrant un poids supplémentaire et des économies de coûts.
Après avoir satisfait à toutes les exigences de Ford, la première utilisation commerciale du matériau était pour un linteau de toit avant et un panneau de fermeture de plancher avant sur la Ford GT à forte intensité de composite de carbone. supercar.
Il n'est pas surprenant que le préimprégné en fibre de carbone/époxy ait un coût élevé, il est donc préférable pour les véhicules avec des mandats de réduction de masse importants qui peuvent payer un supplément pour des opportunités d'économie de poids importantes.
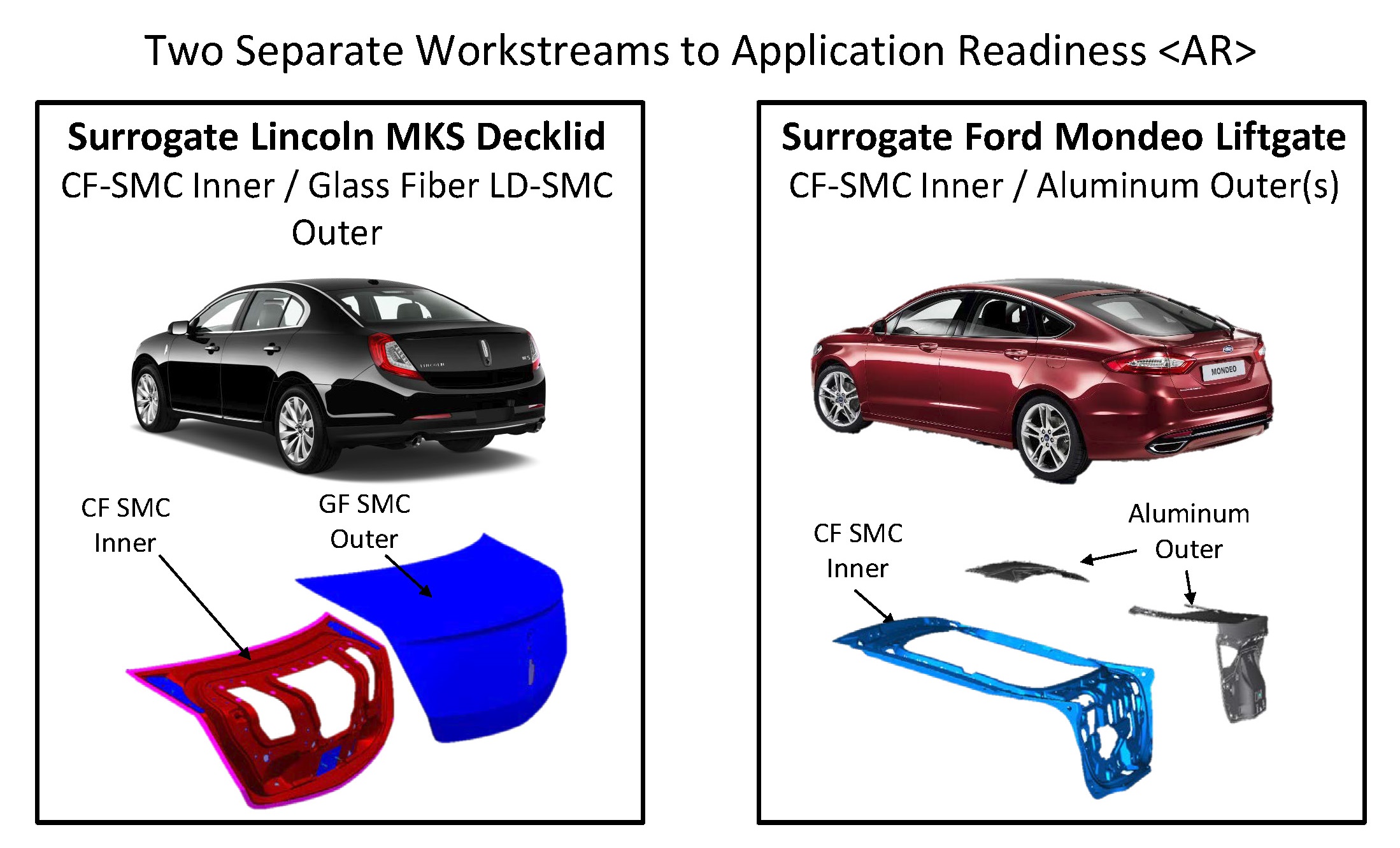
Phase 2/Workstream 1 :couvercle de coffre entièrement SMC
S'appuyant sur les succès du préimprégné, les chercheurs du projet ont ensuite exploré le SMC discontinu renforcé de fibres de carbone avec la nouvelle résine époxy dans des structures 3D complexes avec des fonctions critiques pour la sécurité. Dans un démonstrateur, le SMC en fibre de carbone/époxy a été utilisé comme panneau intérieur/structural d'un couvercle de coffre collé (couvercle de coffre), et dans un autre démonstrateur, il a été utilisé pour le panneau intérieur/structural d'un hayon collé beaucoup plus grand et plus complexe ( hayon/porte avec vitre, moteurs d'essuie-glace, éclairage, etc.). Dans les deux flux de travail, les contraintes de conception d'origine, le matériel, les techniques d'assemblage et les adhésifs structurels sont restés inchangés. Des cibles mécaniques difficiles d'une résistance à la traction supérieure à 300 MPa et d'une rigidité à la traction supérieure à 40 GPa — comparables à celles du magnésium et de l'aluminium coulés en place — ont été utilisées. Le SMC avait également besoin d'un débit plus élevé que le préimprégné, c'est pourquoi un grade légèrement différent, le VORAFUSE M6400, a été développé.
Pour le démonstrateur de couvercle de coffre, qui représentait une avancée incrémentielle par rapport à la technologie actuelle en verre/SMC, le SMC en fibre de carbone/époxy a remplacé le polyester insaturé renforcé de fibre de verre structurel conventionnel pour un intérieur de couvercle de coffre sur un Lincoln MKS véhicule prototype. Le panneau intérieur en fibre de carbone/époxy SMC a été collé à un panneau extérieur en fibre de verre/polyester SMC à faible densité (LD, 1,25 SG), qui a remplacé un SMC en fibre de verre/polyester de densité standard (1,9 SG). Les anciens et les nouveaux matériaux des panneaux extérieurs étaient compatibles avec la classe A. L'outillage d'origine a été réutilisé pour mouler à la fois l'intérieur en fibre de carbone/époxy SMC et les panneaux extérieurs en fibre de verre/polyester. Le rétrécissement - bien que légèrement différent entre les deux systèmes de résine - était suffisamment proche pour ne pas causer de problèmes d'ajustement et de finition (en d'autres termes, aucun changement dimensionnel significatif n'a été observé).
Le prototypage virtuel a soumis l'assemblage collé à un certain nombre de cas de charge difficiles, notamment la rigidité en torsion, la rigidité des coins avant, la déflexion en cascade et les charges de verrouillage. Des dizaines de panneaux intérieurs et extérieurs ont ensuite été moulés, collés et testés, y compris des impacts arrière difficiles à 89 kilomètres par heure. Les assemblages ont réussi les tests virtuels et physiques sans problème.
La masse du couvercle a été réduite de 30 % (de 10,5 à 7,33 kilogrammes) par rapport à la référence. Cependant, si les budgets avaient permis de rééquiper le panneau intérieur - qui aurait pu être conçu plus mince compte tenu de ses performances mécaniques supérieures à celles de l'opérateur historique - les chercheurs ont calculé que la masse aurait pu être réduite d'au moins 35 % avec des parois de 2 millimètres, et même plus avec des parois de 1,5 mm.
Le SMC en fibre de carbone/époxy a satisfait à toutes les exigences Ford et peut désormais être utilisé sur des plateformes commerciales, bien que le coût soit plus élevé qu'avec un SMC en fibre de verre/polyester conventionnel.
Phase 2/Workstream 2 :SMC/hayon élévateur en aluminium
Pour le dernier projet, les chercheurs se sont tournés vers un scénario vraiment difficile :remplacer le métal léger par de la fibre de carbone/époxy SMC pour produire un assemblage hybride (métal/composite) pour des hayons élévateurs plus grands et plus complexes sur Ford Mondeo véhicules d'essai à cinq portes/hayon. Pour minimiser les modifications apportées aux séquences de construction du véhicule, les chercheurs ont conçu l'assemblage à ajouter à la carrosserie en blanc (BIW) avant le traitement électrophorétique de revêtement antirouille (e-coat) et les cycles de peinture-cuisson associés.
La fibre de carbone/époxy SMC a remplacé le magnésium pour les panneaux structurels/intérieurs qui ont été collés aux panneaux extérieurs en aluminium en place. Comme de nouveaux outillages ont dû être créés pour produire le panneau composite, la pièce a été repensée. L'épaisseur du panneau a été modifiée en fonction des exigences de rigidité/résistance et pour ajouter des nervures. En outre, des renforts métalliques ont été utilisés dans les zones de fixation à forte charge pour les vérins à gaz, les loquets, les charnières et les serrures, ce qui a rendu le panneau composite un peu plus épais, ce que l'espace de l'emballage permettait.
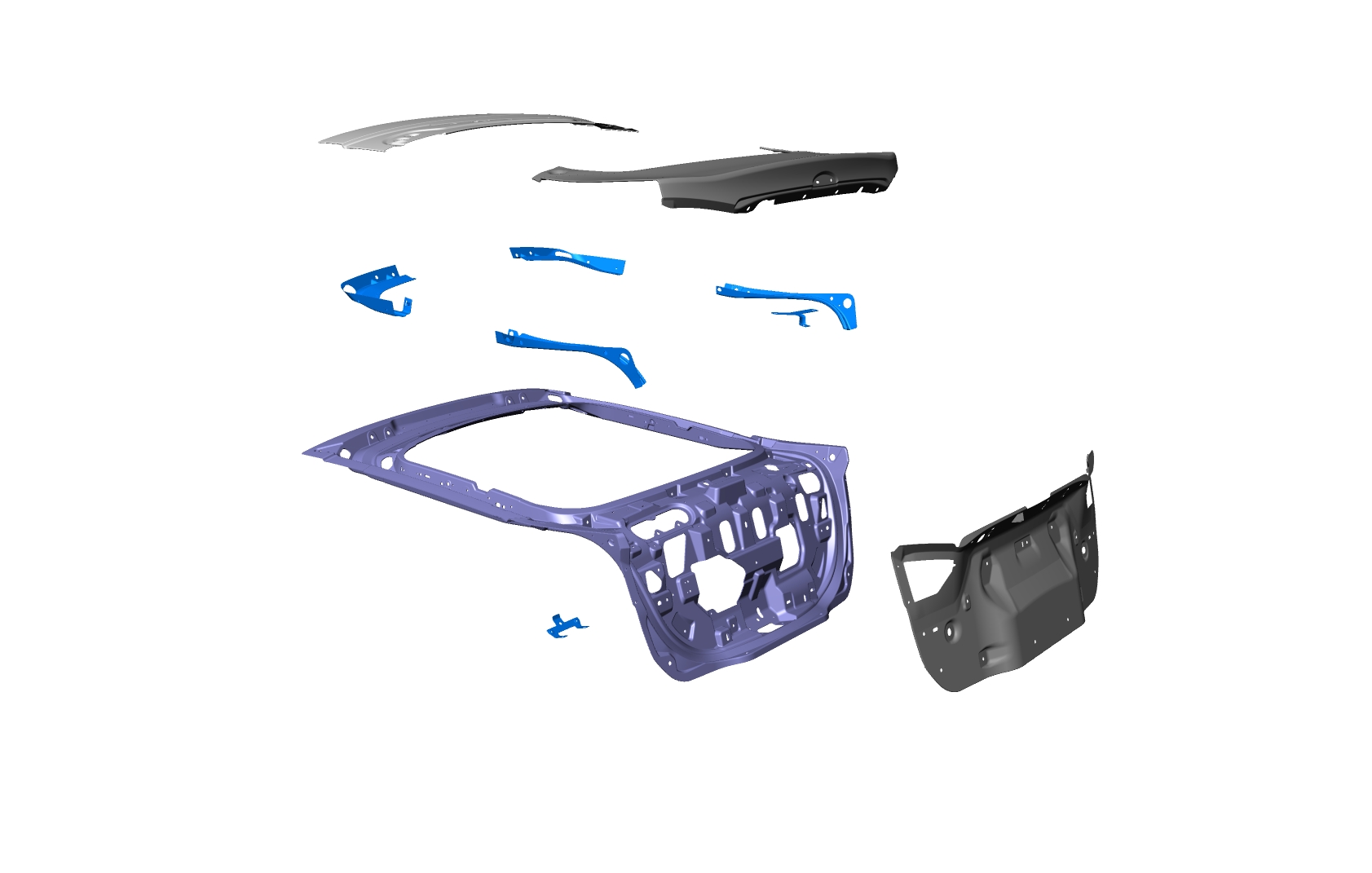
Une vue éclatée du hayon SMC/aluminium (avec quincaillerie métallique) pour la version cinq portes/hayon de la Ford Mondeo. Origine | Ford Motor Co.
Ces assemblages multi-matériaux ont été soumis à des exigences élevées, notamment des charges de torsion et de flexion, une stabilité latérale, une résistance à la corrosion, une durabilité à long terme et des tests de collision arrière. Ils devaient également répondre à des exigences strictes de stabilité dimensionnelle en ce qui concerne les marges et l'affleurement.
Alors que le système hybride a facilement satisfait à la plupart des exigences, il y a eu des problèmes d'ajustement et de finition en raison des écarts de coefficient de dilatation thermique linéaire (CLTE) entre les panneaux intérieurs composites et les panneaux extérieurs en aluminium, ce qui a entraîné une accumulation de contraintes résiduelles dans les joints collés et une distorsion des panneaux après refroidissement. vers le bas. Les travaux ultérieurs avec l'équipe de simulation de l'Université Purdue se sont concentrés sur l'amélioration des prédictions du module, de la résistance et de la cinétique de durcissement de l'adhésif époxy 1K (choisi pour sa capacité à survivre aux températures de couche électronique) dans l'espoir de rétro-concevoir un adhésif qui fonctionnerait mieux. Le gauchissement a été réduit d'un ordre de grandeur, mais a légèrement manqué la cible. Plusieurs solutions sont possibles :un adhésif 2K/à température ambiante ou à induction pourrait être essayé ou un nouvel adhésif à haute température pourrait être développé. À plus long terme, le remplacement de l'aluminium par un composite de fibre de carbone sur le panneau extérieur éliminerait le problème, tout comme la production du hayon hors ligne et son ajout plus tard dans la séquence de construction du véhicule. Cependant, les deux options ajoutent un coût.
Le projet 3.2 est maintenant terminé mais a produit une technologie intéressante, dont certaines - le préimprégné du pilier B et le couvercle de pont SMC - sont prêtes pour le commerce, et dont certaines indiquent des domaines où des travaux supplémentaires sont nécessaires.
« Travailler avec l'IACMI et nos partenaires industriels et universitaires nous a permis de plonger beaucoup plus profondément dans la technologie du premier directeur, de développer la science fondamentale et de tirer parti d'une base de connaissances beaucoup plus large que nous n'aurions pu le faire seuls », résume Patrick Blanchard, chef du projet 3.2, systèmes polymères de pointe, recherche et innovation Ford. « Nous sommes impatients d'identifier de nouvelles opportunités commerciales et activités de R&D pour continuer à travailler avec nos partenaires IACMI. »
Résine
- Appareils en fibre de carbone pour votre maison
- Trois principales utilisations de l'impression 3D en fibre de carbone dans la fabrication
- Utilisations innovantes de la fibre de carbone
- La fibre de carbone dans les applications automobiles
- 5 utilisations amusantes des feuilles de fibre de carbone
- Matériaux :PP renforcé de fibre de verre et de carbone pour l'automobile
- Hexion présente une solution époxy à deux composants pour la production de composites aérospatiaux
- Le motoryacht à foils impressionne en fibre de carbone/époxy
- Série conçue pour la chaîne de production automobile